The new primary smelting technology employs a Double Sided Blown (DSB) electric furnace fitted with 3 electrodes . Refractory lined furnace walls are cooled by copper water jackets. The DSB feeds material comprising of sulphide copper concentrate, coal and fine quartzite. The raw materials are blended according to the required proportions by Distributed Control System (DCS). The blend is continuously fed into the furnace. Oxygen enriched air is blown through an array of ten tuyères on either longitudinal sides of the furnace. The tuyères are completely submerged in the molten slag phase. Smelting energy is generated by the exothermic reaction, which occurs because of the interaction of sulphides and coal with oxygen. The resulting melt separates into two layers in the hearth section of the furnace. The denser molten matte layer contains copper-iron sulphides below the unwanted upper slag layer which contains waste oxides.
Matte with 55% copper content is periodically tapped through an 80mm taphole which is at an angle with the horizontal. The weight of the melt exerts pressure to the base of the furnace hearth and thus pushing matte upwards through the matte channel. Matte flows via a launder into a ladle and transferred by a matte winch system and overhead crane to one of three tilting Pierce-Smith converting furnaces. Slag is continuously skimmed through the skimbay and gravitates along an inclined launder where it is intersected by a stream of pressurised water granulating, cooling and transporting the slag into a pond. The granulated slag is further cooled in a pond full of water. Cool slag is loaded into a locomotive wagons by a grab crane and transported to the slag dump where it is discarded.
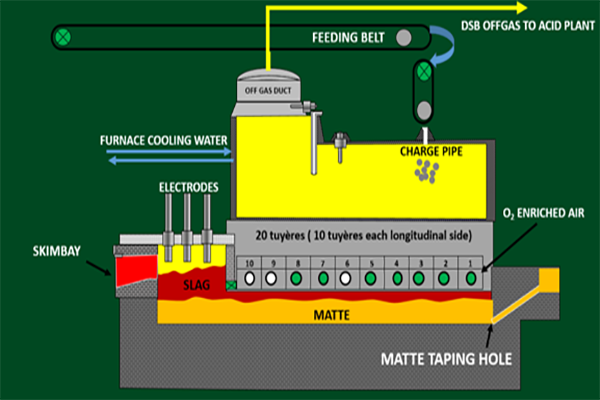