Tankhouse electrorefining process produce 99.99% copper cathode and byproduct anode slime from 99.5% copper anode. Smelter supplies the Tankhouse with two types of copper anodes that are stripper and commercial, with the stripper anodes used to make starter sheet and commercial anodes responsible for cathode deposition. The copper anodes and starter sheets are loaded into commercial sections, which consist of 40 electrolytic cells per section. Voltage is applied across the anode-cathode pair to stimulate copper ions to get electrons and deposited on the cathode surface. Copper loaded cathodes are harvested periodically with desired pull weight and current efficiency. The precious metal from copper anode reports to anode slime settling down to the cell bottom, which is processed through settling tanks, press filters and dried in the oven. As the electro-refining process going, electrolyte requires regular purification and control by adding reagents and bleeding off electrolyte to remove impurities accumulated in the electrolyte, which can negatively influence the cathode quality. The Tankhouse is equipped with the following sub-systems including anode shaping and preparing units, automatic crane, starter sheet stripping & assembling, anode scrap pulling and packing unit, short-circuit monitoring system.
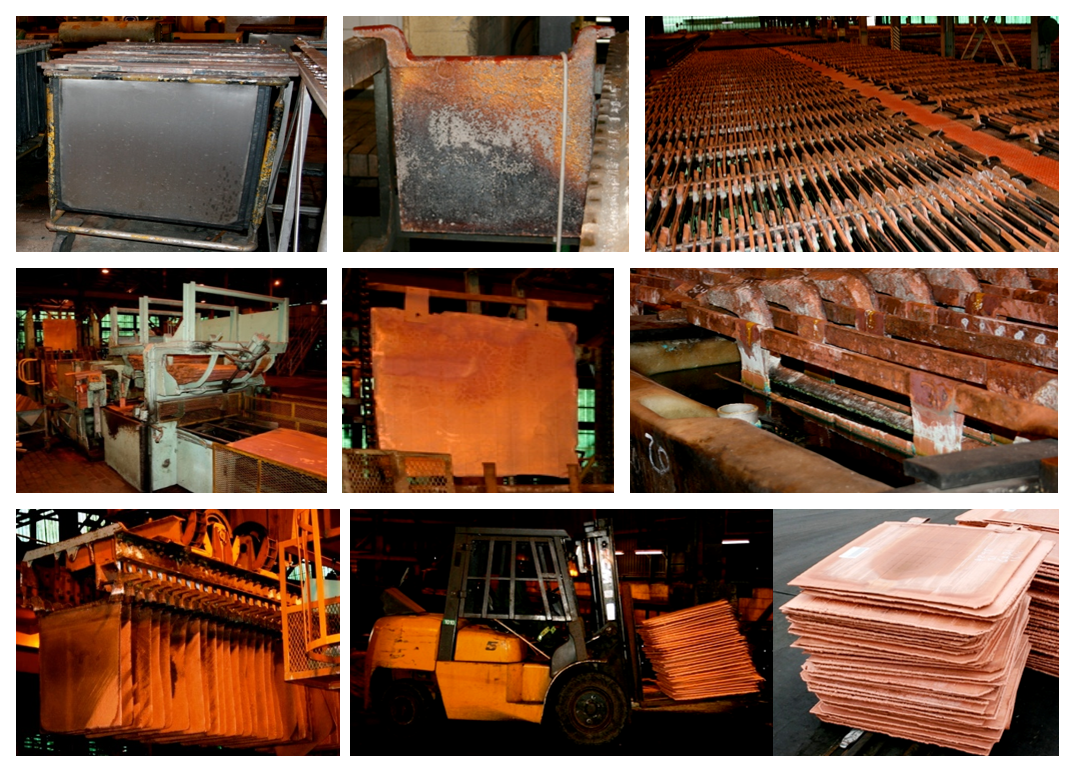